Health, Safety and Incident Risk Management
Health, Safety And Incident Risk Management
Our goal is to establish a culture that prioritizes safety and to implement health, safety, and environment (HSE) requirements, including risk management expectations, that support an incident-free work environment. It takes everyone at the jobsite working together as an interdependent team and adhering to these safe work practices to achieve our goal of being incident-free.
Consistent with our core value around safety and environment and in support of our overall HSE policies, we launched LiveSafe™ across all of our businesses. LiveSafe focuses our attention and actions on making safety personal in everything that we do, whether on or off the job. We are committed to LiveSafe because we value the safety of our people, our families, and our co-workers.
The safety and well-being of our employees and the protection of our environment is a cornerstone, and we are committed to providing a safe, incident-free work environment for all.
As stated in our HSE Policy Statement which applies across our Company and at all facilities and locations, our managers and supervisors are accountable for the safety of our people and are committed to ensuring that they have functional equipment, required personal protection equipment (PPE) and training for their tasks. We have developed Health, Safety and Environment management systems to establish the policies, standards, and procedural requirements by which we conduct our business in order to achieve these objectives. We prioritize health, safety, and environmental control and carefully monitor our performance and adherence to established management system requirements. Our executive management and Board of Directors regularly review and discuss, on at least a quarterly basis, our safety results and trends at the beginning of each regular Board meeting.
We regularly audit and review our HSE performance in all of our businesses. The timing and frequency of these audits is set by an established audit calendar, which is developed considering the type of audit and required frequency. Corrective actions are identified and implemented for any non-conformities observed during the audit. Best practices discovered during these audits and other assurance activities are aggregated and disseminated to our operations teams, HSE professionals, and technical services group so they can be reviewed and implemented across our organization.
Safety and Environment
The safety and well-being of our employees and the protection of our environment is a cornerstone, and we are committed to providing a safe, incident-free work environment for all.
Safety Performance
Due to our operations being primarily onshore and focused in the United States, we measure our safety performance against that of our industry peers who have similar geographical operational footprints. One of the many metrics that we track is our Total Recordable Incident Rate (TRIR). In 2023, our employees worked a total of 20,937,765 man hours.
*This total reflects man hours for all legacy Patterson-UTI entities for 2023 and includes NexTier and Ulterra man hours beginning in Sept. 2023. HSE POLICY Check out our full policy statement here, or go to patenergy.com for more. 0.82
Total Recordable Incident Rate
Ongoing Safety Training
At Patterson-UTI, we prioritize investment in training our employees to be knowledgeable about and responsible for the safe execution of their actions in order to protect themselves, their team members and others. Learning is a core focus and continuous development is a key tenet of our training. Our training programs, both classroom and on-the-job, give our people a clear path for success right from the start. We coach and we mentor. Continuous learning is our way of life.
2023 Training Data | |
Legacy Patterson-UTI Completion | Total |
Number of courses taught | 150 |
Number of training completions | 34,902 |
Number of unique employees trained | 18,375 |
Average training hours per attendee | 8.08 |
Average training hours per unique employee trained | 5.23 |
Competion Services Training Completion | |
Number of instructor led courses taught | 1,099 |
Number of eLearnings completions | 135,337 |
Number of employees completing online training | 13,584 |
Number of employees completing optional courses | 1,395 |
Average eLearning training hours per employee | 8.9 |
Legacy Patterson-UTI Courses | Total |
LiveSafe | 4,786 |
Well Control Certification - Drillers and Supervisors | 601 |
Leadership | 700 |
U.S. Code of Business Conduct and Ethics | 5,947 |
Diversity, Inclusion and Respect for Non-Managers | 4,275 |
Diversity, Inclusion and Respect for Managers | 1,640 |
Cybersecurity | 2,167 |
Global Anticorruption | 210 |
Competion Services Courses | |
Professional/Leadership | 961 |
Tech Training | 999 |
HSE Training | 3,129 |
Drilling Product Courses | |
Preventing Workplace Harassment | 231 |
Code of Conduct | 236 |
Tech Training | 1,764 |
HSE Training | 835 |
Risk Management | Stop Work Authority
Stop work authority is focused on stopping the job before something is able to escalate and can no longer be controlled, potentially resulting in a significant incident or injury. When stop work authority is utilized, a conversation is held with involved personnel to talk about why it was called, what has changed, and what needs to be modified so work can safely resume.
All of our businesses empower employees with stop work authority. We believe there is no job worth performing if it cannot be performed safely. Safety meetings and briefings are tools we use to identify risks and communicate those risks through safety alerts and bulletins.
Our employees, contractors, and anyone else on our work locations are empowered to stop work to address a safety concern.
Pre-Job Assessments
Our Permission to Work program is a formal system of control for all contract drilling operations, focusing on controlling critical and potentially hazardous operations and outlines the requirements for the Jobsite Manager’s permission to control the job rather than a permit. Each job task is categorized based on a risk assessment associated with the expected scope of work, hazard associated with the job and the appropriate amount of supervision required.
Our Jobsite Manager then verifies the work is ready to begin and gives permission for the job to start by signing the certificate. After completion of the work, the Jobsite Manager must conduct a post job examination of the worksite, close the operation by signing the certificate and conduct a post job review.
Similarly, our Completion Services business follows its PAUSE process, which includes pre-job checklists and job safety analyses before beginning a job. Completing the PAUSE process and hazard assessment is the responsibility of the Jobsite Manager to help ensure incident free operations and is required to be completed prior to engaging in any task.
The goal of these programs is to help us to control the outcome of each job in a safe, efficient manner. Additionally, our system dictates that an appropriate level of risk assessment be completed prior to performing any operation, and dynamic risk assessment be conducted throughout the operation.
Employee Safety Orientation
We require all field-based employees to take Employee Safety Orientation (ESO). Courses include content on Behavior-Based Safety, Hazard Awareness, Safe Systems of Work, Permission to Work, Time Out for Safety, Energy Isolation, HAZCOM, Material Handling, etc.
ISO Certifications
Our pressure pumping business, which maintains approximately 1,000 vehicles in its fleet, launched a driver safety program to promote safe driving practices in 2022.
Driving Safety
2023 marks the Completion Services business’s first full year with Samsara fleet monitoring systems with great results. Utilizing the advanced driver assistance system technology coupled with internal management processes, allows a proactive approach to our employees and others on the ride. Samsara offers real time warnings to drivers and gives the Company behavioral reports that monitor driving behaviors, such as speeding, quick turns and accelerations as well as alerting the appropriate leadership and support parties for performance management.
Maintaining Our Standards
In our drilling and Completion Services businesses, we routinely evaluate contractors to ensure they meet both Patterson-UTI and our customers’ HSE requirements. In our evaluation process, we review and evaluate contractors prior to hire based on HSE performance statistics, selected HSE policies and procedures, questionnaires, and thirdparty evaluation systems. This evaluation process assists us in screening contractors and maintaining our standards. We monitor existing contractors’ safety performance in assessing whether to continue contractor relationships.
Industrial Hygiene Management Policy
We understand the importance of occupational health, as our employees work in many different environments and conditions. We assess these conditions with industrial hygiene management policies that include: respiratory protection, hearing protection, HAZCOM, climate and environmental condition risk mitigation and industrial hygiene monitoring.
We perform industrial hygiene monitoring to identify, evaluate, and document potential exposure to biological, chemical, and physical hazards at Patterson-UTI jobsites and facilities, which includes:
- Workplace hazard assessments conducted at each yard, shop and rig location
- Crew houses monitored and inspected on a periodic basis
- Periodic occupational exposure monitoring
- Temperature monitoring on location
Incident Review and Comprehensive Incident Management System (IMS)
In our Drilling and Completion Services businesses, our policies require that any incident, including any near hit, is reported to the manager on location and recorded and tracked in our Incident Management System (IMS). The incident is then reviewed and classified based on its actual and potential severity. The purpose of the IMS program is to establish the requirements for how workrelated incidents and near hits are reported, investigated, corrected, recorded, and communicated. The IMS program also helps enable assignment of corrective actions and preventative actions, as well as identifying opportunities for communication of lessons learned.
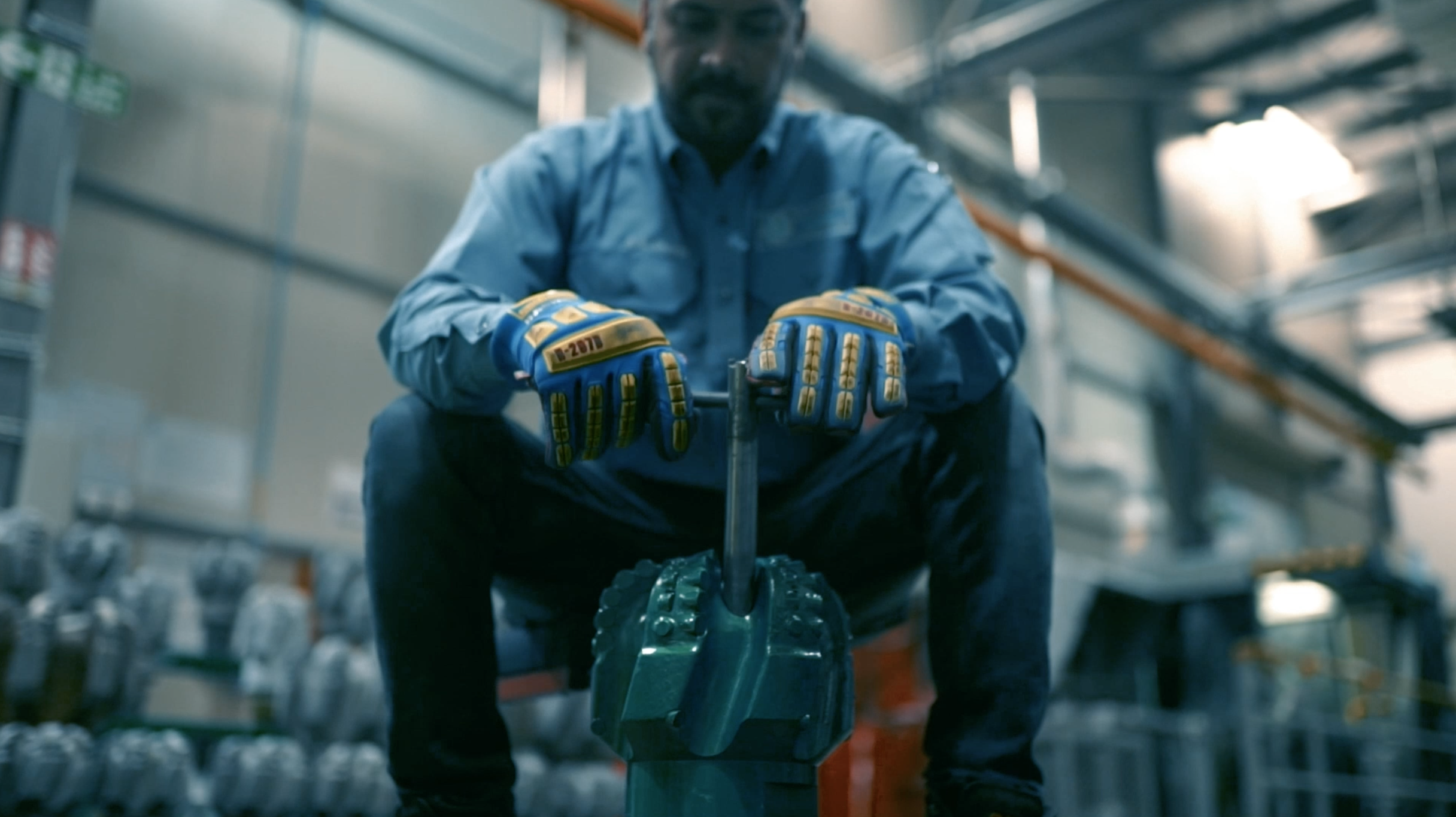
Cloud-Based Management and Feedback System
We expect our Drilling Services employees to actively participate in crafting our processes and procedures, and we encourage everyone to approach their supervisor with suggestions for improvement and, in our contract drilling business, to use our readily available computer-based feedback system. Our cloud-based Management System houses the policies, procedures, and standards that define the Company’s expectations and requirements related to safety and operational processes. The Management System also includes technical standards, forms, inspections, audits and other supporting documentation for daily operations.
Our employees have the opportunity to provide direct feedback and suggestions using our Policy Improvement Request (PIR) process. If there is a need for clarification, revision, or the expansion of existing processes, employees can submit their requests through this online system.
Cornerstones for Life
The “Cornerstone for Life” rules provide our employees with extra focus on potentially high-risk activities where we believe failure to follow rules could lead to a much higher probability of serious injury or fatality.
Cornerstones for Life are tailored for our Drilling Services and Completion Services businesses to highlight critical safety expectations at all jobsites. Patterson-UTI employees, contractors and visitors are required to adhere to these rules. Some examples of Cornerstones for Life in our businesses include:
- Utilize our permission to work process without fail.
- Follow our fall protection policy.
- Properly isolate energy to equipment / lockout tagout when appropriate.
- Follow appropriate management of change protocols.
- Take appropriate precautions when working around overhead power lines.
- Ensure that appropriately sized tubular handling equipment is utilized.
- Follow our safe driving and fit for duty policies.
Emergency Planning and Response
We have policies and procedures in place to address emergency planning and emergency response. For example, our locations regularly have onsite safety drills, including severe weather and well control drills. Our cloudbased Management System contains policies covering safety and emergency response topics, including detailing requirements for conducting drills, including frequency and type of emergency response drills. We have also developed enhanced communication abilities with employees to be able to promptly alert employees regarding severe weather events or other potential crises through our Company’s intranet(s) and in some instances, texting or notification capabilities.
Management of Change
Our Management of Change policy provides a managed systematic approach designed to ensure, to the extent possible, that health, safety, and environmental risks are identified, understood, communicated, controlled, and approved prior to implementing certain changes to our operating procedures and policies. The policy requires that certain operating procedural changes be reviewed and approved before implementation to reduce the potential for risks resulting from such changes.